The History of Forging
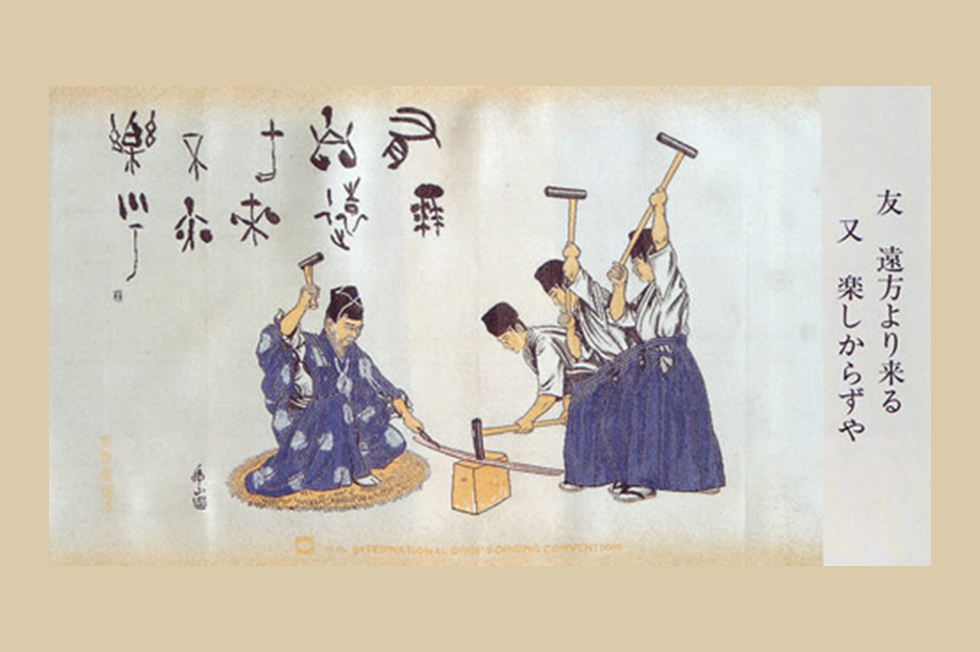
Forging is a process of preparing iron by beating until a certain shape is created. The Chinese character 鍛 means to forge an object until it is strong and resilient. Before 4000B.C. in Egypt and Mesopotamia, people forged copper, gold, and silver to make ornaments, objects of worship, and weapons.
The ancient forging technology developed for hundreds of years. The forging technology for weapons evolved, as well as for household commodities and farming tools such as hoes and axes.
Around 470 A.D., materials brought from the mainland china were introduced, strongly influencing the current technology. As a consequence, diverse tools proliferated since the introduction of these eccentric materials. Around 500 A.D, the production of iron in Chugoku, San-in, Kita Kyushu and Tohoku regions began. This led to the spread of carpenter tools, hunting equipment, horse riding harnesses, and body armor used in war.
Towards the end of the Heian Era, Japanese sword craftsmanship reached to the level of profound perfection. The Japanese swordsmith boasted unparalleled sharpness. This forging technology went on its skill to create to become a renowned and cultivated historical tradition.
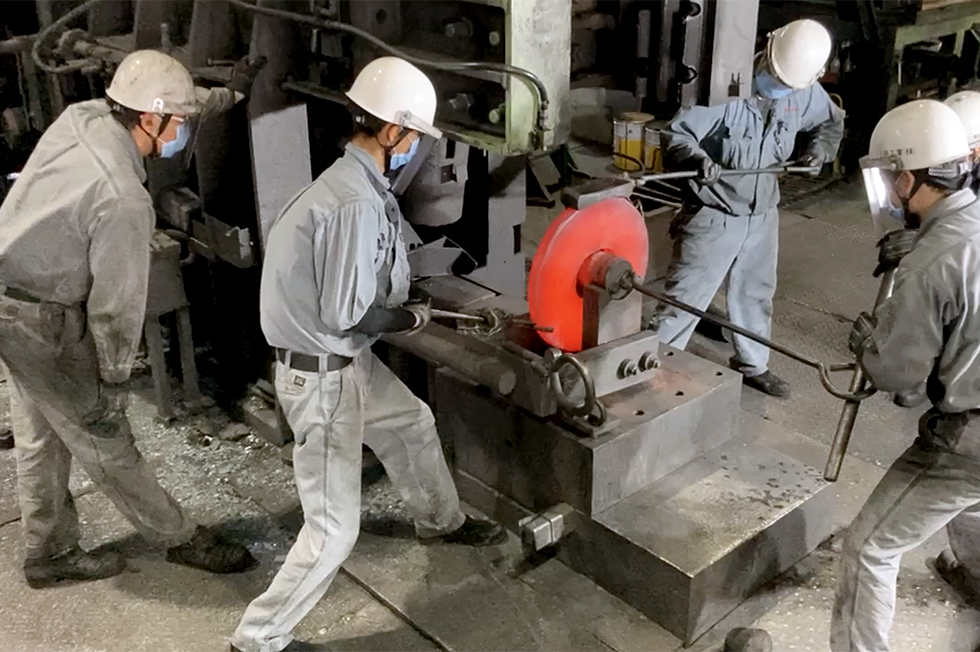
Our Technology
Melting iron and pouring it into shape is universally known as casting. It is relatively easy to make iron sheets and other complex shapes; however, the drawback is that they crack easily.
Where does the strength come from in forging? Japanese swords or well-sharpened kitchen knives are not forged by means of melting. They are beaten by a hammer and manufactured so that the desired shapes are made.
It is a time consuming process, and, it is sometimes rather difficult to attain the desired shape. Nevertheless, the strength lies in the impeccable sturdiness of a product that does not break easily.
The unyielding metal is produced by steady forging throughout production.
We have a history of constantly thinking about what we can do with forging to “solve our customers’ problems,” and as a result, we have developed our own unique technological capabilities.
“How to manufacture commercial parts with high quality and cost merit?”
“How to achieve this speedily and in a short period of time?”
Our company-wide focus on these issues has led to our current strengths.
For example;
-All of current parts can now be made by forging alone.
-Parts that used to be made separately can now be made in a single piece
(integration of multiple parts).
By doing so, we are able to see beyond the imagination of our customers and make proposals to them.
Specifically, we are good at the following;
- 01.
It is possible for us to design and produce even without drawings, as long as there is an actual product (even one that does not retain its original form). - 02.
We handle the entire process in-house, from proposal design, mold making, prototype production, to mass production. - 03.
Forge molding is possible to a shape close to the casting area even though it is a forging. - 04.
Cold forming is environmentally friendly by eliminating the formation of any coating such as zinc phosphate film (bondellite). - 05.
Precision forging is possible even in small lots. This can contribute to cost reduction. - 06.
We are particular about inspection accuracy to minimize losses.
Our staff have wealth of experience and technology, and also faculties including inspection machines of which there are only a few dozen in Japan.
Thus we improve production efficiency and exceed customers’ expectations.